Employee Safety and Health
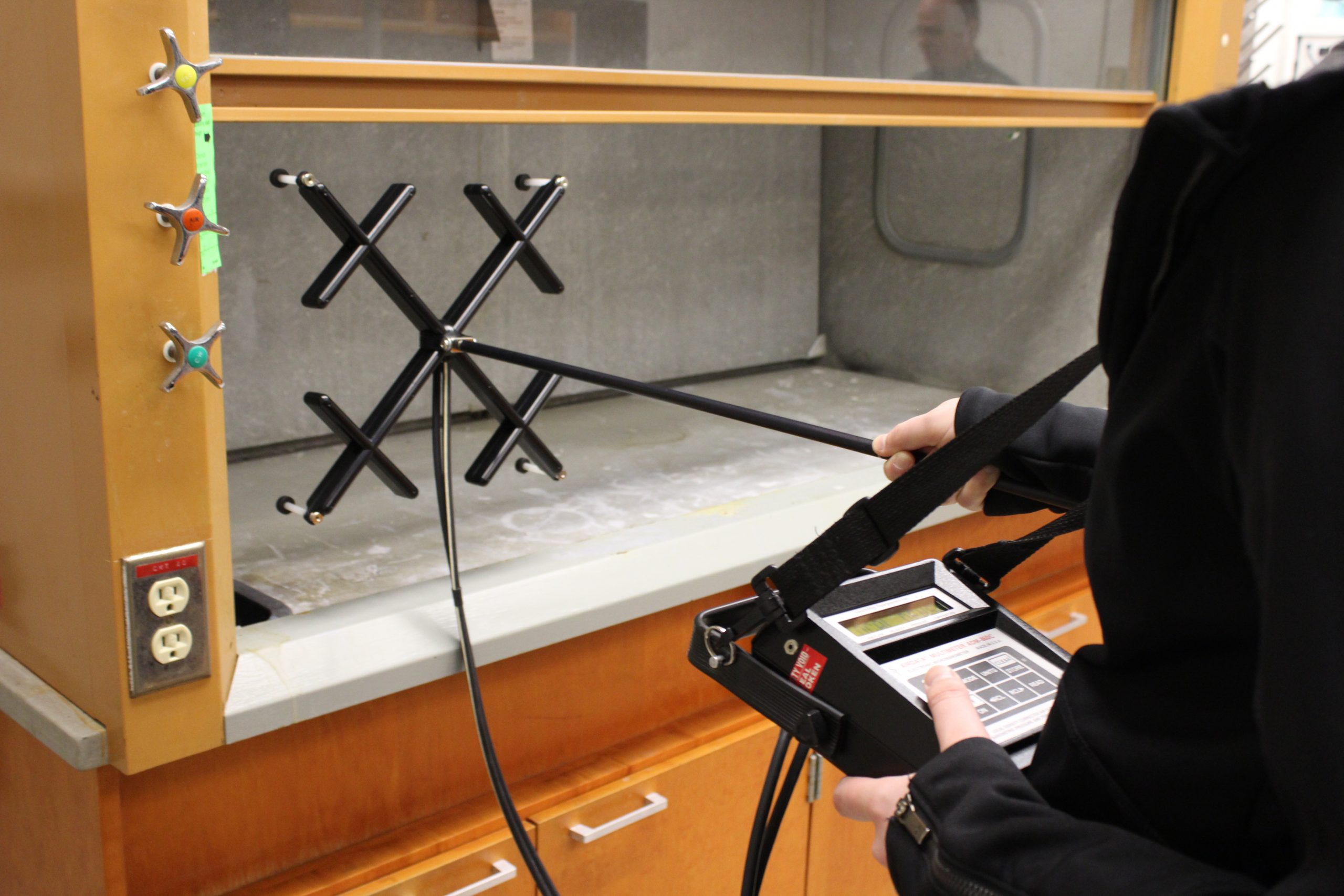
Employee Safety & Health programs help protect the safety and health of our campus community at all levels – including student events, faculty, and staff. The programs listed on the left provide information and resources for some of the specific safety issues facing campus workers.
The Illinois Fire Service Institute (IFSI) coordinates the campus Automated External Defibrillators (AEDs) program. For more information please click here.
Special events on campus may require risk reduction measures to enhance the safety of participants. Guidelines and reference materials are available to help campus units reduce or eliminate potential hazards which may cause injury, illness, or property loss.
Temporary Food Service
Temporary food service in campus buildings or other facilities is recorded by the Division of Safety & Compliance (S&C) so that a full and proper investigation can be performed in the event of a foodborne illness. S&C must be notified of the date, location, type of food, and means of handling and serving. The primary concern is perishable food that has potential to spoil, especially foods that should be served hot or cold. If you have events where only foods such as coffee, sodas, cookies and donuts are served, S&C does not need to be notified. Food handling advice is given to groups preparing and/or selling food for fundraisers and other social activities.
When you hire a caterer to provide food for your event, you must verify that the caterer is able to provide safe food. It is important that caterers be licensed and inspected by their local health department.
Groups requesting to provide food service in University space for their event need to complete the Food Service Request Form. Questions concerning food safety should be directed to the Division of Safety & Compliance, Occupational Safety & Health at (217) 265-9828 or oshs@illinois.edu.
Should your event require or request a food sanitation inspection or training, associated fees will be the responsibility of the host group.
Please review the Temporary Food Service Guidelines before hosting your event.
The Safety and Compliance division maintains the Chemical Fume Hood Surveillance Program as part of the university’s effort to comply with the OSHA Laboratory Standard. A campus-wide laboratory fume hood survey is conducted on an annual basis. References and guides for the safe operation of chemical fume hoods are provided in this section.
The regulations for chemical fume hood evaluations and safety are from the Occupational Safety and Health Administration (OSHA), 29 CFR 1910.94 and 29 CFR 1926.57 and can be located at http://www.osha.gov through their links to Laws and Regulations and then to Standards.
Background
Chemical fume hoods are equipped with a fan in the duct work that generates air flow from the front to the back of the hood. Air escapes through slots or baffles at the back of the hood. The air flow captures vapors and prevents them from diffusing into the room. Hoods are designed so that the air velocity at the plane of the sash is optimal for capturing vapors when the sash opening is no greater than the maximum operating position (for vertical opening sashes) or the test opening (for horizontal opening sashes). For vertical sliding sashes, the maximum operating height of the sash is typically 18 inches; a larger opening limits the performance of the hood. The opening should be minimized on hoods with horizontal sliding sashes and the user should work with one sash directly in front of them with their arms on either side of the sash. Maximum sash openings are identified using blue stickers. On combination hoods that include both the vertical and horizontal sashes, it is best practice to put the vertical sash all the way down before opening and using the horizontal sashes. Opening the sash beyond the optimal position will dramatically lower the air velocity and allow vapors to escape into the room. Blocking the airflow with large equipment in the hood can also lead to insufficient vapor capture and potential exposure.
A person standing in front of the hood also disrupts the airflow, generating eddy currents. Vapors within those currents may escape into the room. Eddy currents drop off at about six inches into the hood.
Hood Inspections
A campus-wide Chemical Fume Hood Surveillance Program is coordinated by the Occupational Safety and Health Department (OSH). Fume hood face velocity is measured annually by OSH. If the velocity falls within the established operating range established by the campus of 80 and 120 linear feet per minute (fpm), or within the operating range established by the manufacturer and verified through as-installed containment testing, the hood will receive a green Chemical Fume Hood Evaluation tag bearing the date of the inspection. Approved operating flow range and maximum approved sash opening are listed on the white Chemical Fume Hood Operating Parameters sticker that is placed on the fume hood.
If research work in your fume hoods is critical, the F&S Sheet Metal Shop can provide annual testing and immediate repair by requesting a Preventative Maintenance work order through the F&S Service Office.
If the face velocity is outside the range listed on the Chemical Fume Hood Operating Parameters a WARNING sign will be posted on the sash and the previous year’s green tag will be removed. If a WARNING sign is present, contact your facility manager for Repair, OSH and DRS cannot initiate repair of failing hoods. Do not use hazardous material in the hood until it has been repaired and is working properly. The F&S Sheet Metal Shop will re-test the hood as part of the repair work.
The hood can function properly only if its integrity is not compromised. A hood with missing side panels or cracked sashes will not provide adequate exposure control.
Because the status of the chemical fume hood can change anytime, continuous air flow indicators are recommended. New chemical fume hoods must be equipped with air flow monitoring devices which will alert the user if there is a problem with air flow. For older hoods without air flow monitoring devices, a simple visible test to ensure flow into chemical fume hoods and other ventilating devices is to tape a tissue to the hood and note its movement when the exhaust fan is turned on.
Safe Work Practices
To reduce the risk of exposure as much as possible, adhere to the following work practices:
- Open the sash or sashes only as much as is required to perform your work comfortably. Never open it beyond the indicated position when hazardous chemicals are present. Position the sash to maximize protective shielding.
- Verify that the chemical hood is drawing air. Check the flow monitor if present, or hold a Kimwipe in the hood and check its movement. Note: Do not let go of the wipe. Wipes sucked into the ductwork will block airflow and may cause damage requiring expensive repairs.
- Perform all work at least 6 inches into the hood and do not store items near the opening where they interrupt airflow and pose a spill hazard.
- NEVER put your head in the hood when hazardous chemicals are present.
- Do not position large equipment or containers of chemicals in the back of the hood where they block airflow. Elevate equipment by placing it on blocks, jack stands, or legs so that air can flow underneath to the bottom baffle slot. To store items in the back of the hood, install shelves to elevate containers (see Fig 3). Keep inside the hood only what needs to be there and remove everything that can be stored outside.
- Route service connections under the airfoil and secure all loose and dangling electrical cords, tubes and tubing with tie-raps, twist ties, or rubber bands.
- Discontinue work and close all containers with hazardous chemicals if the alarm sounds. If possible, mute the alarm, put an out-of-order sign on the hood, and contact your department business office to arrange for repair.
- When the hood is not in use, keep the sash at a six-inch opening. This will significantly reduce energy consumption and the sash will act as a shield in the event of an unexpected release. A small opening is required to serve as air exhaust for the laboratory.
- Ductless fume hoods are not recommended due to limitations on chemical use within the hoods and required maintenance. OSH and F&S do not provide support for ductless fume hoods. Verification of proper operation and maintenance/repair is solely the responsibility of the owning department.
Questions?
If you have questions about properly using chemicals in your fume hood or storing chemicals please email the Division of Research Safety, DRS@illinois.edu.
If you have questions about annual fume hood face velocity testing please email the F&S Occupational Safety & Health department, OSHS@illinois.edu.
Review the Ergonomics Self-Help Guide to help you make adjustments to your workstation.
The purpose of an ergonomics program is to assist campus units in promoting safety and preventing soft tissue injuries.
Other specific program information, including office ergonomics (computer workstation) assessments and training, should be obtained from the Department of Occupational Safety and Health, 217-265-9828 or safetyandcompliance@illinois.edu.
The Division of Research Safety (DRS) coordinates the campus Hazard Communication (Hazcom) program. For more information please click here.
The University of Illinois is committed to creating, promoting, and maintaining a safe and healthy workplace for faculty, staff, and student employees. When workplace injuries do occur despite prevention efforts, it is important to minimize the impact and cost to the injured worker, the sponsoring department, and the university. Information on reporting an employee injury can be found on the Workers’ Compensation Reporting Procedures and Responsibilities webpage. For injury reporting, utilize the First Report of Injury/Illness form. Follow the instructions on the form for proper completion and submission. Contact the University Office of Worker’s Compensation and Claims Management at workcomp@uillinois.edu or 217-333-1080 with questions.
In the event of a fatality, in-patient hospitalization, amputation, or physical loss of an eye, the following information shall be immediately communicated to the Division of Safety and Compliance via phone at 217-255-2106:
- Building name and address where incident took place;
- Date and time of incident;
- Date and time of notification to campus official;
- Number of fatalities or hospitalized employees;
- Name and contact number of person making the report; and
- Brief description of the incident.
Illinois OSHA Injury Reporting Requirements
The university is required to report certain significant injuries to the Illinois Occupational Safety and Health Administration (OHSA) immediately upon discovery. The F&S Safety and Compliance division has established a procedure to ensure that the university meets its reporting requirements.
Please print and display this poster in your facility, which provides the steps for proper reporting procedures. The document should be placed where other information important to employees, such as mandatory federal and state workplace regulations, is displayed.
Thanks for your assistance with distributing this information across campus.
The Safety and Compliance division maintains the Medical Surveillance Program as part of the university’s effort to comply with regulations from OSHA, NIH, IDPH, and other agencies which require that employees, who may be exposed to harmful substances through their job duties, be enrolled in a medical surveillance program. Employee health screenings are conducted by the occupational medicine department of the currently contracted medical provider.
Departments needing assistance should contact Safety and Compliance, 217-265-9828.
The regulations for medical surveillance will be found in the substance-specific regulations from the agency involved (for example, the OSHA asbestos standard).
Review the Hearing Conservation Program and complete the request for a sound level survey if you believe there are high noise level operations or machines in your work area (e.g., hold your arm straight out and snap your finger, if you cannot hear the snap high noise levels may exist).
PURPOSE
The University of Illinois Urbana-Champaign, through the Division of Safety and Compliance, Occupational Safety and Health Department (OSH), has established this Hearing Conservation Program to protect the health of university students, faculty and staff and to assure compliance with State and Federal occupational safety and health standards.
This Program provides the minimum requirements for campus units to develop and implement unit-specific written standard operating procedures (SOPs) to complement and meet the requirements detailed in this program, including completion and submission of Appendix A to OSH.
RESPONSIBILITIES
Occupational Safety and Health (OSH)
OSH is responsible for the administration of this program, which includes determining the need for hearing protection based on the hazard assessment and hearing protector selection. An OSH program coordinator is designated to provide guidance, regulatory interpretation, and oversight for this program and to review this Program annually.
Deans, Department Heads and Directors (Campus Units)
Campus Units shall designate a Responsible Person that will be charged with implementing this Program and Unit-Specific SOPs.
Campus Unit Responsible Person
The Responsible Person shall work with Campus Unit Supervisors to identify personnel that may be required to wear hearing protection and shall keep OSH apprised of new potential hazards entering the work area for both new-hire personnel and for those having a change in their job duties. In addition, personal protective equipment (PPE) assessments of work processes and tasks, described in the University’s Personal Protective Equipment Program; must be completed to ensure that all personnel within their unit affected by this Program receive proper training. The Responsible Person shall ensure that Unit-Specific SOPs are reviewed annually.
Supervisors of Affected Employees (Supervisors)
Supervisors and Principle Investigators (PIs) are responsible for enforcing proper use, care, maintenance and storage of hearing protectors for the wearers under their responsible charge in accordance with this Program and Unit-Specific SOPs. They shall assist in the development and annual review of Unit-Specific SOPs. They shall ensure that all their personnel who must undergo audiometric testing do so on an annual basis. The testing is at no cost to the individual.
Affected Employees
Affected faculty, staff, and students, herein called users, are responsible for using hearing protection when required by the specified work activity and ensure that the protectors are worn, cleaned, stored, and maintained according to the provisions of this Program, Unit-Specific SOPs, and manufacturer instructions. Those required to undergo annual audiometric testing shall do so in accordance with this Program.
PROCEDURES
Hazard Evaluation and Identification
The selection of appropriate hearing protection shall be made only after determining the potential exposure of University personnel to high levels of noise. A noise assessment of the workplace shall be conducted; including area surveys and/or noise dosimetry (see Appendices C, D, and E). OSH can conduct the noise assessment or assist the unit in identifying other providers.
Campus personnel that suspect occupational noise exposure can report it by submitting a Noise Assessment Request. Noise exposure monitoring shall include an area survey and personal monitoring.
Program Evaluation
This Program will be reviewed annually by OSH. The written Unit-Specific SOPs shall be reviewed and updated by the respective Campus Unit at least annually and more frequently as hazards, tasks, procedures and/or equipment change.
The Personal Protective Equipment (PPE) Program helps employees identify work situations requiring the use of PPE, and trains them in the proper selection and use of PPE and documentation of this information. Persons overseeing or visiting job sites must wear appropriate personal protective equipment.
PURPOSE
The University of Illinois Urbana-Champaign (University), through the Division of Safety and Compliance (S&C), Occupational Safety and Health Department (OSH), and the Division of Research Safety (DRS), has established this Personal Protective Equipment (PPE) Program (Program) to protect the health and safety of university students, faculty, and staff and to ensure compliance with State and Federal occupational safety and health standards.
PPE devices are not to be relied on as the only means to protect against hazards. The best approach is to abate the hazard first through engineering and administrative controls (change in process, elimination of process, chemical substitution, etc.). If hazards cannot be controlled with these methods, PPE should be used to provide worker protection. This program will be used in conjunction with other University policies and procedures involving the protection of students, faculty, and staff.
RESPONSIBILITIES
Occupational Safety and Health (OSH) and Division of Research Safety (DRS)
Campus safety units (OSH and DRS) are responsible for the administration of this program as it applies to student, faculty, and staff exposures to hazards (e.g., electrical shock, noise, falling/flying objects, chemicals, biohazardous materials, lasers, radioactive materials, etc.). The Campus safety units can, upon request, provide or assist with general awareness training, hazard assessments, and recommendations for appropriate selection of PPE. Additionally, the Campus safety units will provide regulatory interpretation and review this Program annually.
Deans, Department Heads, and Directors (Campus Units)
Deans, Department Heads, and Directors will demonstrate a commitment, both fiscal and managerial, towards the implementation of the PPE Program. They will establish budgetary support for this program for their individual department(s) and ensure the PPE Selection Guidelines are implemented and maintained within their department(s).
Supervisors of Affected Employees
Supervisors are responsible for contacting OSH or DRS with questions about the type of PPE required for a task and conduct or arrange for the appropriate selection and fitting of PPE. Supervisors are responsible for ensuring a Job Hazard Assessment (JHA) or other hazard assessment documentation that requires PPE is developed and maintained for activities under their supervision. Supervisors must ensure employees receive training on the proper selection, storage, use, and maintenance of PPE when employees they supervise are required to use such equipment. Supervisors must also ensure retraining.
Supervisors are responsible for conducting or arranging for PPE-specific training, documenting, and maintaining training records. Supervisors are also responsible for supplying the appropriate PPE to employees and ensuring it is worn according to the training provided. Supervisors must assure the requirements of this program are observed with respect to hazard surveys, testing, training, and record keeping.
Employees
Employees are responsible for reporting to the supervisor any operation or job for which they suspect that PPE may be needed. Employees are also responsible to attend training on PPE as required by this program. Further, they are responsible to use PPE in accordance with instruction and training received as necessitated by job hazard assessments. Employees should not use any PPE with deficiencies and should report any deficiencies or malfunctions to a supervisor. Employees should notify their supervisor if they experience a noticeable change in health while wearing their PPE or experience a potential problem with their PPE.
PROCEDURES
The Hazard Assessment
An assessment of the workplace is used to determine if hazards are present, or are likely to be present, and necessitate the use of PPE. When conducting a hazard assessment, a task is identified, investigated and potential hazards determined. Potential hazards may be physical or health-related. Examples of physical hazards include moving objects, fluctuating temperatures, rolling or pinching objects, electrical connections and sharp edges. Examples of health hazards include overexposure to harmful dusts, chemicals, or radiation. The hazard assessment may be conducted for an individual employee, performing a single task, or a group of employees if all the employees perform an identical task. The assessment should be documented.
Hazard Assessment Documentation
A workplace hazard assessment must be performed through a written certification that identifies the workplace evaluated, the person certifying that the evaluation has been performed and the date(s) of the hazard assessment. The Job Hazard Assessment form (Appendix A) is one tool that satisfies the assessment process has been completed as required by regulations. This assessment assures that potential workplace hazards and appropriate controls, including PPE, have been identified. Completed assessment forms shall be maintained by the department and available to the employee. All hazard control selection decisions, including the selection of PPE, must be communicated to the affected employees.
PPE Selection Guidelines
PPE must be selected that will protect the employee from each hazard identified in the assessment that cannot be controlled through the use of engineering or administrative controls. The PPE Worksheet (Appendix B) will assist in this process.
PROGRAM EVALUATION
This program will be reviewed annually by OSH.
Appendices:
Review the Respiratory Protection Program and complete the Request for Respirator Use if you think you may need a respirator.
PURPOSE
The University of Illinois at Urbana-Champaign (University), through the Safety and Compliance division, Occupational Safety and Health department (OSH), has established this Respiratory Protection Program to protect the health of university students, faculty and staff and to assure compliance with state and federal occupational safety and health standards.
This program provides the minimum requirements for unit-specific respiratory protection programs. It is expected that campus units will utilize this Respiratory Protection Program to develop unit-specific standard operating procedures (SOP), including completion and submission of Appendix A to OSH.
RESPONSIBILITIES
Occupational Safety and Health (OSH)
OSH is responsible for the administration of this program, which includes determining the need for respiratory protection based on the hazard assessment, respirator selection, initial training, and annual fit-testing. OSH maintains copies of all records for services provided by OSH about this program. An OSH program coordinator is designated to provide guidance, regulatory interpretation, and oversight for this Program and to review this Program annually.
Deans, Department Heads, and Directors (Campus Units)
Campus units shall designate a Responsible Person that will be charged with implementing this program and unit-specific SOPs.
Campus Unit Responsible Person
The Responsible Person shall work with Campus Unit Supervisors to identify personnel that may be required to wear a respirator and shall keep OSH apprised of new potential hazards entering the work area for both new-hire personnel and those having a change in their job duties. In addition, personal protective equipment (PPE) assessments of work processes and tasks, described in the university’s Personal Protective Equipment Program, must be completed to ensure that all personnel within their unit affected by this Program receive medical clearance, and proper training and fit-testing. The Responsible Person shall ensure that Unit-Specific SOPs are reviewed annually.
Supervisors of Respirator Wearers (Supervisors)
Supervisors and Principle Investigators (PIs) are responsible for enforcing proper respirator use, care, maintenance, and storage of respirators for the wearers under their responsible charge in accordance with this Program and Unit-Specific SOPs. They shall assist in the development and annual review of Unit-Specific SOPs. They shall ensure that all their personnel who wear a respirator receive training and fit-testing on an annual basis. They must also ensure that all personnel have had a medical evaluation as dictated by the medical provider. The medical is at no cost to the individual.
Respirator Wearers
Affected faculty, staff, and students, herein called respirator wearers, are responsible for obtaining a medical clearance to wear a respirator, to be fit-tested, and to receive training. The respirator wearer shall use the respirator when required by the specified work activity and ensure that the respirator is donned, cleaned, stored, and maintained according to the provisions of this Program, Unit-Specific SOPs, and manufacturer instructions.
PROCEDURES
Request for Respirator Use
A Request for Respirator Use must be submitted to OSH for any individual wanting to wear a respirator. The request will be evaluated through a review of procedures, established engineering and administrative controls, and exposure monitoring. All costs associated with exposure monitoring will be at the expense of the requesting unit. Upon completion of the evaluation, OSH will provide a written determination of the need for a respirator and assist in the selection of appropriate respiratory protection.
PROGRAM EVALUATION
This program will be reviewed annually by OSH. The written Unit-Specific SOPs shall be reviewed and updated by the respective Campus Unit at least annually and more frequently as hazards, tasks, procedures and/or equipment change.
Appendices:
Useful Resources:
OSHA 1910.134 Respiratory Protection Standard
NIOSH Respirators Information
High temperatures and humidity stress the body’s ability to cool itself, and heat illness becomes a special concern during hot weather. Although these conditions are most prevalent in the summer, working in any hot environment, including an unventilated room, can present heat-related hazards.
Exposure to freezing and cold temperatures for extended periods of time may cause serious health problems such as trench foot, frostbite and hypothermia. In extreme cases, including cold water submersion, exposure can lead to death. Employees working outside in the winter months and those working walk-in freezers are especially vulnerable.
Safety & Compliance can conduct hazard evaluations of temperature extreme environments, make recommendations for engineering and administrative controls, provide training, and assist campus units in creating written programs and site-specific Standard Operating Procedures to protect employees against temperature extremes.
Documents